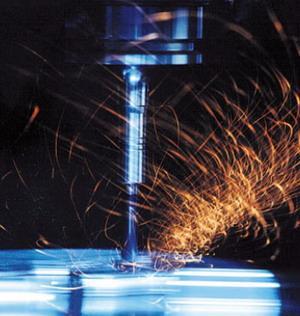
This technology breaks the monopoly of foreign companies in the field of high-end tool coating technology, improves the localization rate of high-grade coated tools, and lays a solid foundation for key users such as automobiles and aviation to increase production efficiency and reduce production costs.
Zhuzhou Diamond Tool made a breakthrough in key coating technology, reduced the cost of cutting a key part of the engine block of a car engine by 30%, and raised the localization rate of a typical user, Chery Automobile's engine processing tool, from 20% to 47% is of great significance in replacing imports and meeting the urgent needs of key industries.
It is an indisputable fact that China is a big country. However, there is still a gap between China's CNC cutting tool technology and foreign countries, which is highlighted in the basic research of advanced coating manufacturing and coating technology. The successful application of new Ti-Al-XN coating technology broke the monopoly of foreign strong companies in the field of high-end cutting tools, laid a solid foundation for improving the localization rate of tools, and created conditions for better meeting the needs of key industries. Has significant economic and social benefits.
Carry tool core technology: The machine is called the machine that makes the machine. If the high-end CNC machine tool is a modern industrial civilization artwork, then the high-end carbide precision tool is a diamond on the artwork, and the sparkle of the diamond comes from a precision coating of a few microns thick on the tool surface.
Coated tools have high surface hardness, good wear resistance, chemical stability, resistance to heat and oxidation, low coefficient of friction, and low thermal conductivity. The reason is that the coating material acts as a chemical barrier and a thermal barrier, which reduces the diffusion and chemical reaction between the tool and the workpiece, thereby reducing the wear, making the tool life improve by 3 to 10 times, and the cutting speed by 20% to 100%. A thin layer of paint carries the core technology of the tool.
At present, the proportion of coating tools in cutting tools has reached 80%. As foreign companies occupy a monopoly position in the field of high-end cutting tools, the status of tools and their core coating technologies is increasingly valued in China's CNC machine tool special projects. Breakthroughs in technology have been included in a number of research projects.
Catch up with the international advanced level of similar products Zhuzhou Diamond Company independently developed the new coating technology of Ti-Al-XN is not easy. In the initial introduction of the coating production line, zizhu drilling can only produce ordinary Ti-N and Ti-Al-N coatings. Through digestion and absorption, researchers have developed nano-structured Ti-Al-N coatings that have improved performance over ordinary Ti-Al-N coatings, but still cannot meet the needs of the tool industry. Under this circumstance, Zhuzi set up an R&D team to take advantage of the special platform for the construction of precision tools and innovative capabilities as an opportunity to carry out centralized research and development of new high-performance coatings.
After extensive experiments, the research team chose the optimal Ti-Al-XN coating, which has higher oxidation resistance and hardness than Ti-Al-N coating, but its cutting performance is comparable to that of Ti-Al-N. No significant improvement. In order to understand why the coating performance does not achieve the expected results, the R&D team first peeled the new coating off the substrate and ground it into a powder for differential scanning calorimeter analysis to analyze the phase structure evolution and spinodal decomposition of the coating at high temperature. process. Through unremitting efforts, the research team prepared an optimized nanocomposite multilayer coating nc-TiAlN/Si3N4.
It is understood that the Ti-Al-XN new coating technology has obtained nine patents and all patents for inventions. The hardness of PVD coating products is higher than 40GPa, achieving superhard effect. After oxidation in an air atmosphere at 1100°C for 10 hours, the coating is still not fully oxidized. After tempering at 1100°C, the hardness of the coating can still maintain more than 40GPa, and the bond strength with the substrate exceeds 90N. During the same period, the thickness of the self-developed CVD coating α-Al2O3 reaches 10μm, the coating bond strength exceeds 80N, and the cast iron is machined. Speed ​​up to 500 meters. Compared with products used by users, the mold processing industry has reached or exceeded the international advanced level of similar products.
Solar Cells,Monocrystalline Solar Cell,Full Power Solar Cells,Poly Solar Cells
ZHONGWEI CITY YINYANG NEW ENERGY , http://www.yinyangnewenergy.com