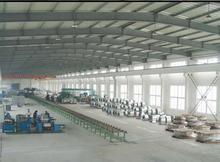
Heat conduction devices, appliances or components include radiators, heating plates, air conditioners, and automobile water tanks. They are used in a wide range of applications and are involved in aerospace, transportation, automobiles, construction engineering, electronic appliances, electric energy, household appliances, and furniture. All military and civilian industrial sectors and all aspects of people’s lives have played a role in human civilization, social progress, and economic development.
The characteristics of aluminum alloy heat transfer materials The history of the application of heat conduction devices has been a long history, so the use of its materials has a history of thousands of years, but various materials are constantly changing and developing. From the material point of view, the radiators that are still commonly used in the world are: steel radiators, aluminum radiators, copper radiators, cast iron radiators, and other materials or composite radiators. From the use point of view, there are currently functional radiators and decorative radiators. Aluminum alloys have a small density, high specific strength, good electrical and thermal conductivity, excellent plasticity, can be processed into a variety of complex shapes, can be surface processed into various colors, good corrosion resistance, long service life, recyclable A series of advantages such as good sex, therefore, has gradually become the main heat-conducting material, especially in the aspect of function type radiator aluminum material has already become the mainstream.
Aluminum radiators have the following features compared to similar products of other materials:
1. Corrosion resistance, long service life. A thick layer of solid oxide film can be formed on the surface of aluminum alloy material, which can be used in heating water with pH ≤ 9 or in automobile water tanks for a long time, and aluminum radiators with special surface treatment can be used at pH ≤ 12 Medium and long-term use of materials.
2. It can be used for various surface treatments, with many varieties, no solder joints, strong decorative, beautiful and durable, and can meet people's individual requirements.
3. Use safety, high pressure. Because of the specific strength and specific rigidity of aluminum alloy, it is much higher than copper, cast iron and steel. Even in the case of thin thickness, it can withstand sufficient pressure, bending force, pulling force and impact force. During the handling, installation and use, no damage will occur.
4. Lightweight for easy installation and handling. When the heat dissipation is the same, its weight is only eleventh of the cast iron radiator, one-sixth of the steel radiator, and one-third of the copper radiator, which can greatly save the transportation cost, reduce labor intensity, and save installation time.
5. Simple installation and easy maintenance. Since the aluminum alloy has a low density and can be processed into parts of various shapes and specifications, the cross section of the aluminum radiator is large and regular, and product assembly and surface treatment can be performed in one step. The construction site can be directly installed, which saves a lot of installation. cost. Maintenance is also convenient and inexpensive.
6. Energy saving, low cost of use. When the radiator center distance and the heat transfer temperature is the same, the aluminum heat sink than the cast iron radiator heat dissipation is 2.5 times higher, but also because of the appearance, can not add heating cover, can reduce heat loss by more than 30%, cost reduction10 More than %, the heat sink of aluminum radiator is slightly inferior to copper radiator, but the weight can be greatly reduced. Since the price of aluminum is only 1/3 of the price of copper, it can greatly reduce costs.
From the above, it can be seen that the aluminum radiator is a new energy-saving and environmentally-friendly radiator. With beautiful appearance, large heat dissipation area, good heat collection effect, corrosion resistance, light weight, easy installation, handling and maintenance, it has good social and economic benefits and can completely replace traditional cast iron, steel and copper radiators. The market prospect is very broad.
Classification of automotive heat transporters and their aluminizing trends Automotive heat transfer systems include automotive air conditioners, water tanks, oil coolers, intercoolers, and heaters. The automotive heat exchanger is located at the front of the car and is subject to rain, salt evaporation from the road surface, exhaust gas from the car, sand, dust, and mud, as well as repeated cold and hot cycles and periodic vibrations. These pose serious challenges to the selection of heat exchangers, corrosion protection, and joining techniques. The traditional heat exchangers are made of copper. However, the development of automobiles has become more lightweight. At the same time, low-cost processing and assembly technologies have emerged, making the application of aluminum heat exchangers successful in automobiles.
From the viewpoint of the characteristics of aluminum, the heat exchanger is the most suitable part for manufacturing with aluminum. The quality of aluminum radiators is 37% to 45% lower than that of copper radiators, the price of copper materials is about 60,000 yuan/t, and the price of aluminum materials is 28,000 yuan/ton. The processing fees for both are almost the same. As a result, automotive air conditioners in Japan and the United States use almost exclusively aluminum. The aluminumizing rate of radiators reaches 90% to 100% in Europe, 70% to 80% in the United States, and 50% to 60% in Japan. China is also making heavy use of aluminum radiators, aluminum internal coolers, and oil coolers. , heater cores, etc. are also rapidly spreading.
In light of the need for lightweighting, miniaturization, improved heat dissipation, and corrosion protection, the automotive heat exchangers have been actively improved in structure, ranging from corrugated serpents to thin-walled parallel flow, DeLong cups, and singles. Box type and so on. Improvements have also been made in materials, such as the use of Al-Cu-Mn-Cr-Zr alloys and Al-Mn-Si-Fe alloys to improve the strength reduction due to thinning; The chemical composition was used to further improve the corrosion resistance; a multilayer composite material (Al-Mn coating structure) was developed; the composition was adjusted by brazing to achieve the purpose of corrosion prevention. These improved technologies have reached the practical stage.
As automotive radiators are becoming smaller, lighter, high-performance, low-cost, and durable, aluminum radiators have become dominant in the confrontation between copper and aluminum materials, and various types of radiators for automobiles have been applied to aluminum products. Conversion. At present, all kinds of radiators on automobiles are the most used systems for deformed aluminum alloys, such as engine radiators, oil radiators, intercoolers, air conditioning condensers, and evaporators, etc. The main aluminum materials used are various types of plates. , belts, foils, composite belts (foil), extruded round tubes, flat tubes and multi-hole flat tubes, welded round tubes and flat tubes, have many specifications and high quality requirements.
Automotive heat transfer aluminum alloy composite materials choose automotive composite heat sink materials for the manufacture of water tanks, condensers and evaporators. Automotive radiators and air conditioning condensers are composed of fluid pipes and heat sinks, and are assembled by mechanical expansion or brazing. Its structural materials are mainly aluminum alloy porous harmonica tubes, flat tubes, high-precision thin-walled tubes, and aluminum alloy three-layer composite heat-dissipating foil strips.
The three-layer composite aluminum alloy brazing foil should meet the requirements of light weight, corrosion resistance, good thermal conductivity, high strength, good formability, ability to be brazed, precious metal savings, and comprehensive performance and versatility. In order to achieve the above requirements, especially the requirements of brazing and corrosion resistance, the aluminum alloy composite foil is a 4xxx alloy (skin material) coated on both sides of a 3xxx core material, and the coverage rate is 10% to 16%. The brazing of the composite foil does not need to be applied with brazing material, so that the aluminum alloy composite foil has good brazing performance and processing performance, thereby simplifying the manufacturing process of the radiator and the condenser, reducing the production cost, and achieving the lightness of the automobile. The purpose of the quantification.
The base alloy should use aluminum alloy with high melting point, suitable high temperature strength, good bonding with solder during brazing, small bending deformation and little effect on solder diffusion, and moderate moderate strength and corrosion resistance in use. Most foreign countries use 3xxx alloy and 6xxx alloy as matrix. In view of the fact that China's imported equipment brazing process is gas shielded welding, Nocolok brazing and vacuum brazing, taking into account that the 3xxx series alloy has excellent mechanical properties, brazing and corrosion resistance, and most of the use of units using 3003 Alloy and Zn-added X313 alloy matrix composite plates, therefore, selected 3003 and X313 as the base alloy.
The coating alloy as the brazing material coating the base alloy should have a low melting point, good fluidity, and good wettability. The coating alloys commonly used abroad are 4xxx alloys, such as X414, 4343, 4045, 4047, and 4N43 alloys suitable for gas shielded welding and Nocolok brazing; and 4004, 4104, and 4N04 alloys suitable for vacuum brazing.
In order to meet the requirements of domestic production lines, 4043, 4045, 4N43, X414, 4004 and 4N04 alloys were selected as cladding alloys. In the brazing process of the composite plate, the fluidity, wettability, gap filling ability, eroding property, and joint strength of the cladding alloy represent the quality of brazing. Therefore, to strictly control the content of the main elements of the cladding alloy, the main elements of the alloy are as follows:
The role of Zn: First, the corrosion potential of the alloy can be reduced, the greater the amount of added, the more potential reduction, stamping after the heat sink as the anode preferential corrosion, thereby protecting the medium channel; Second, reduce the alloy surface oxide film strength, The surface is easily peeled off and the surface is completely eroded to achieve the purpose of suppressing pitting corrosion. However, if the Zn content is too high, the corrosion rate of the heat sink is too fast, which will cause the heat sink to lose its heat dissipation effect and reduce its service life.
Effect of Si element: Al-Si alloy has the lowest melting point of 577°C near the eutectic point, which is its advantage as a brazing material. After compounding, the Si element diffuses to the matrix alloy due to the concentration gradient, so that the solid solubility of the Mn element of the matrix decreases as the Si content increases, and an anode strip rich in α[Al(MnFe)Si] dispersoid is formed, thereby The potential difference between the Al and the second phase in the substrate is changed so that the corrosion preferentially occurs in the subsurface layer of the substrate. Simultaneously, Si can change the fluidity of the brazing filler metal, uniform the microstructure, and improve the brazing quality.
The role of Mg elements: Mg in the cladding alloy is an indispensable metal activator and getter to ensure vacuum brazing quality. At the same time, it has a certain influence on the corrosion resistance of the composite plate. Corrosion tests show that the addition of Mg elements reduces the corrosion potential of the coating alloy, accelerates the corrosion rate, and has a certain resistance to pitting corrosion.
Automotive heat transfer aluminum alloy composite belt (foil) production process technology The main difference between the rolling and finishing of composite aluminum plate with foil and the general plate and foil rolling is: the core material need to be prepared separately and rolled coated leather material Plates; they need to be cleaned, using conventional acid-base etching, in order to completely remove the oxide film, but it can also be cleaned with cleaning agents, although the oxide film can not be removed, but it is better for the environment.
The core and skin material pairing is to place the Al-Si alloy plate on the core material ingot, and they can be welded together or not, but welding is still better to improve the yield. The argon arc welding can be used to weld the front end and the right and left sides substantially, but it is not necessary to weld it tightly and the end is not welded. The reduction rate of hot-press welding should be small, so that it can be welded best.
There are many factors affecting the selection of three-layer composite brazing foils, of which the brazing method is the key to the selection of materials. Different grades of composite foils for cores and skins have different specific uses. The alloys have different elemental contents depending on the brazing process. The materials have to meet multiple performance requirements, and the performance is sometimes restricted to each other. The actual use requires comprehensive trade-offs.
The brazing process of the automotive heat exchanger assembly shall have good anti-sagging performance in addition to the good mechanical properties, corrosion resistance and brazing performance of the three-layer composite aluminum alloy foil used as a wave cooling band. Otherwise, at high temperatures around 600°C, high temperature softening deformation is likely to occur during brazing, affecting the performance of the radiator.
At home and abroad, there is no uniform test standard for the sag resistance of composite aluminum brazing foils. Tests have shown that under certain conditions of core and skin materials, the cold working rate after annealing is the main factor that affects the anti-sagging ability of the composite foil. Adding zirconium to the core material alloy helps to improve the anti-sagging ability.
Automotive heat-transporting aluminum composite belt (foil) has a promising prospect With the rapid development of the automobile industry, especially the progress of modern vehicle lightening, China's automotive heat-transmitting aluminum alloy composite belt (foil) has also achieved rapid development. In the late 1980s, domestic companies such as Dongcao and Southwestern Aluminum began to develop heat-transfer aluminum materials, but they basically focused on imports. In the middle and late 1990s, some domestic universities and enterprises started R&D and achieved certain results. In 1996, the heat transfer company in Sapa, Sweden, established a professional production base for heat transfer materials in Shanghai, which has enabled China to embark on the road of large-scale production. Since then, Sapa II, Wuxi Yinbang, Alcoa (Kunshan), Weifang Sanyuan, Sasin Aluminum, Zhongxing Aluminum, Guanlv Aluminum, Yuncheng Aluminum, Northeast Light Alloy, Southwest Aluminum and other companies have built Plant or increase production capacity. So far, there are nearly 30 manufacturers in the country with a production capacity of around 500,000 t/a. In 2010, the domestic aluminum composite tape (foil) was more than 300,000 t/a, which basically could meet the development needs of the domestic auto industry and some of them were exported.
Heat-transporting aluminum alloy composite tapes (foil) are mainly used in the automotive industry, and have evolved with the modernization and lightweight development of the automotive industry. At present, the world’s auto production is 80 million units/a, and the number of vehicles is 800 million. In 2010, China produced 18 million vehicles and had 80 million vehicles, which grew at a rate of 8%. If an average of 7kg of aluminum alloy composite tape (foil) is consumed per vehicle, then the world needs more than one million tons per year. However, China may exceed 500,000 t/a. Coupled with the needs of other industries, the market prospect of aluminum alloy composite tapes (foil) is very considerable.
Simple Shower Cabin,Shower Enclosure,Glass Shower Door
Freestanding Bathtub Shower Panel Co., Ltd. , http://www.chbathtub.com