**1. Material Factors**
**1.1 Bulk Density**
The bulk density of the material plays a crucial role in granulation efficiency. Generally, the higher the bulk density, the better the granulation yield. Therefore, when formulating feed, it is essential for nutritionists to not only consider the nutritional requirements but also the physical properties of the ingredients. A higher bulk density ensures better flowability and compaction during the granulation process, which ultimately improves production efficiency.
**1.2 Particle Size**
The particle size of the raw materials significantly affects the granulation process. Smaller particles increase the specific surface area, allowing for faster moisture absorption, which aids in water regulation and enhances granulation yield. However, if the particle size is too fine, the resulting pellets may become brittle, affecting their quality. On the other hand, overly large particles can increase wear on the press rolls and stamper, leading to higher energy consumption and lower yield. For pig feed, the ideal particle size should pass through a 3 mm sieve, while chicken feed should pass through a 3.5 mm sieve, with at least 80% passing through a 1.18 mm sieve.
**1.3 Moisture Content**
The moisture content of the material before conditioning has a direct impact on the granulation process. If the moisture level is too high, it reduces the amount of steam that can be added during conditioning, which affects the temperature rise and, consequently, the quality and yield of the final product. High moisture can also lead to material slippage between the ring die and the pressure roller, potentially causing blockages. To avoid these issues, the moisture content of the material before conditioning should generally be below 13%.
**1.4 Material Composition**
**1.4.1 Protein Content**
Materials with high protein content tend to have greater plasticity after heating, increasing viscosity and improving granulation yield. However, if the feed contains high levels of non-protein nitrogen (such as urea), the granulation yield may decrease due to reduced binding properties.
**1.4.2 Starch Content**
High-starch ingredients are easier to granulate under high temperature and moisture conditions, leading to improved yield. In such cases, the conditioning water should be between 16% and 18%, and the conditioning temperature should exceed 80°C. If the starch is already gelatinized (e.g., dried corn), the granulation yield will drop, so it’s better to avoid drying the raw materials when possible.
**1.4.3 Fat Addition**
Adding a small amount of fat (0.5% to 1%) can reduce machine wear and improve the flow of material through the die holes, thus increasing granulation yield. However, exceeding 2% fat can make the particles too soft and difficult to form. It's recommended to add 30% of the total oil in the mixer and 70% during the granulation stage.
**1.4.4 Crude Fiber**
An appropriate amount of crude fiber (3% to 5%) helps bind the particles together, reducing dust and improving granulation yield. However, if the fiber content exceeds 10%, it can weaken the bonding, increase mechanical wear, and reduce the yield.
**1.4.5 Minerals**
Inorganic minerals typically lack cohesive properties and can negatively affect granulation. When inorganic content is high, adding a binder like molasses can improve the granulation performance and increase yield.
**1.4.6 Heat-Sensitive Ingredients**
Ingredients like lactose or whey powder increase viscosity when heated, which is beneficial for granulation. However, temperatures above 60°C can cause coking, blocking the die holes. To prevent this, warm water is often used for conditioning.
**2. Operational Factors**
**2.1 Conditioning Moisture**
After conditioning, the moisture content of the material should ideally be between 15% and 16.5%. If the moisture is too high (over 18%), the material may slip between the die and roller, reducing yield. If it's too low (below 14%), excessive friction can occur, also lowering output.
**2.2 Roller-Die Gap**
The gap between the press roller and the ring die is critical. The ideal range is 0.05–0.3 mm. If the gap is too large, the material layer becomes uneven, reducing yield. If it's too small, wear increases. A simple way to check is to turn on the press roller and listen for a slight squeak.
**2.3 Die Hole Finish**
New ring molds often have iron filings or oxides inside the die holes, which must be polished to ensure smooth operation. Polishing involves cleaning the holes, applying grease, and using abrasive mixtures to improve surface finish. After polishing, more than 90% of the die holes should be free of blockage.
**2.4 Feeding Scraper Condition**
A worn feeding scraper can reduce the amount of material entering the pressing zone, leading to lower yield and increased powder. Regular inspection and replacement of the scraper are necessary to maintain efficiency.
**2.5 Die Hole Blockage**
Blockage in die holes is usually caused by poor granulation performance or improper cleaning after use. If blocked, the die can be cleaned with a drill bit or soaked in oil and heated for removal.
**2.6 Friction Coefficient**
The friction between the material and the die/roller affects how well the material is pressed. Too little friction causes slipping, while too much prevents ejection of the pellet. This depends on formulation, conditioning, and machine design.
**2.7 Feed Rate**
Even with optimal settings, if the feed rate is too low, the granulator cannot operate at full capacity. Ensuring an adequate and consistent feed supply is essential for maximizing output.
**2.8 Cooling Process**
Proper cooling of the pellets is important to prevent them from becoming too loose or breaking during handling. If not cooled adequately, the particles may break, increasing dust and reducing yield. Cooling time and air volume should be adjusted accordingly. The final pellet temperature should not exceed room temperature by more than 3°C.
**3. Machine Installation and Accessories**
**3.1 Mold Opening Rate**
The opening rate of the ring mold directly affects production. A larger hole diameter allows for a higher opening rate, which increases granulation output. However, the strength of the mold must still be maintained.
**3.2 Die Hole Shape**
Straight-hole ring dies are suitable for most compound feeds, but for high-fiber feeds, tapered-hole dies are more effective. Choosing the right die shape can significantly improve yield.
**3.3 Roll-to-Die Diameter Ratio**
A larger roll-to-die diameter ratio improves the angle at which the material enters the pressing zone, reducing backflow and increasing yield. The ratio should generally be greater than 0.4.
**3.4 Scraper Positioning**
Improperly positioned scrapers can cause material to be pulled out of the die, reducing yield and increasing dust. The scraper should be installed 2–3 mm away from the die and not extend beyond the cutting groove.
**3.5 Die Hole Aspect Ratio**
The depth-to-diameter ratio of the die hole influences both yield and particle hardness. For high-starch feeds, a higher aspect ratio (9.5–12.5) is preferred, while heat-sensitive materials require a lower ratio (4.8–8.0). Adding 1–2% fat may allow for a larger aspect ratio.
Double-concave Cylinder Lens
Cylindrical lenses have at least one surface that is formed like a portion of a cylinder.Cylindrical lenses are used to correct astigmatism in the eye and in rangefinders, to produce astigmatism,stretching a point of light into a line.They are available in either plano-concave or plano-convex configurations. Plano-Concave Cylindrical lenses have a negative focal length and are used for image reduction or to spread light. Plano-Convex Cylindrical lenses have a positive focal length, which makes them ideal for collecting and focusing light for many imaging applications.
Some styles of cylindrical lenses have antireflective coatings to increase the transmission of light through the lens. Fused silica cylinder lenses are ideal for demanding laser machining and medical applications.
Plano-convex cylinder lens,Plano-Concave Cylinder Lens,Double-Convex Cylinder Lens,bi-concave cylinder lens,Meniscus Cylinder Lens, Rod Cylinder Lens ,Achromatic cylinder lens are available.
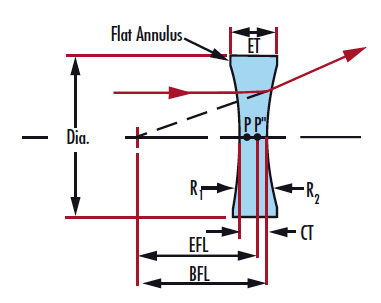
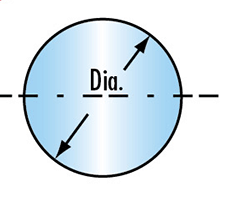
Â
Â
Specification of our cylinderical lens as follow:
*Material: BK7,Ge,UV-grade fuse silica(JGS1,JGS2,JGS3)or other optical materialsÂ
*Dimension Tolerance: +0.0 -- -0.1mmÂ
*Center Thickness: +/-0.1mmÂ
*Focal Length Tolerance: +/-1%
*Surface Quality:20/10Â
*Surface Figure: lambda/2 at 633nm on plano sideÂ
*Clear Aperture>90%
*Chamfer: 0.25mm at 45 degree typicalÂ
*Coating Optional
Double Convex Lens,Bi-Concave Irregular Cylindrical Lens,Double-Concave Cylindrical Lens,Dcv Cylindrical Lens
China Star Optics Technology Co.,Ltd. , https://www.csoptlens.com