**1. Material Factors**
**1.1 Bulk Density**
The bulk density of the material plays a crucial role in granulation efficiency. Generally, the higher the bulk density, the better the granulation yield. Therefore, when formulating feed, it's essential for nutritionists to consider not only the nutritional requirements but also the bulk density of the ingredients.
**1.2 Particle Size**
Materials with fine particle sizes have a larger specific surface area and absorb moisture more quickly, which is beneficial for water regulation and increasing granulation yield. However, if the particles are too fine, they may become brittle, affecting the quality of the final product. On the other hand, overly large particles can increase wear on the press rolls and stamper, raise energy consumption, and reduce yield. For pig feed, the particle size should pass through a 3 mm sieve, while chicken feed should pass through a 3.5 mm sieve, with at least 80% passing through a 1.18 mm sieve.
**1.3 Moisture Content**
Excessive moisture in the raw material reduces the amount of steam that can be added during the granulation process, which affects the temperature rise and, consequently, the yield and quality of the pellets. High moisture content also makes conditioning difficult and increases the risk of material slipping between the ring die and the pressure roller, leading to blockage. Ideally, the moisture content before conditioning should be below 13%.
**1.4 Material Composition**
**1.4.1 Protein Content**
High-protein materials tend to have greater plasticity and viscosity after heating, which improves granulation yield. However, high levels of non-protein nitrogen, such as urea, can lower the granulation yield.
**1.4.2 Starch Content**
Feed with high starch content granulates well under high temperature and moisture conditions, resulting in higher yield. In such cases, the conditioning water should be between 16% and 18%, and the temperature should exceed 80°C. If the starch isn't fully gelatinized, the pellets may become brittle and fail to form. It’s better to avoid using dried grains like corn, as they can reduce granulation yield.
**1.4.3 Oil Addition**
Adding a small amount of oil (0.5% to 1%) helps reduce machine wear and improve pellet flow through the die, thus increasing yield. However, adding more than 2% can cause the pellets to become too soft and lose their shape. To optimize this, it's recommended to add 30% of the total oil at the mixer and 70% at the granulator.
**1.4.4 Crude Fiber**
An appropriate level of crude fiber (3% to 5%) improves bonding between particles, reduces powdering, and enhances yield. However, if the fiber content exceeds 10%, the adhesion between particles weakens, leading to increased mechanical wear and reduced yield.
**1.4.5 Minerals**
Inorganic minerals typically have poor cohesive properties, which negatively affect granulation. When mineral content is high, a binder like molasses is often added to improve performance and increase yield.
**1.4.6 Heat-Sensitive Ingredients**
Ingredients like lactose and whey powder increase viscosity when heated, which benefits granulation. However, temperatures above 60°C may cause coking, blocking the die holes. Using warm water for conditioning is advisable in such cases.
**2. Operational Factors**
**2.1 Conditioning Moisture**
After conditioning, the ideal moisture content should be between 15% and 16.5%. The material should feel slightly moist when squeezed but not sticky. If the moisture is over 18%, the material may slip between the die and roller, reducing yield. If it's below 14%, excessive friction can occur, lowering production.
**2.2 Roller-Die Gap**
The gap between the roller and the die should be between 0.05 and 0.3 mm. A gap larger than 0.3 mm causes uneven material distribution, while a smaller gap leads to severe wear. To check the gap, turn on the roller and listen for a squeaking sound.
**2.3 Die Hole Finish**
New ring dies often have iron filings or oxides inside the holes. These should be polished before use to reduce friction and increase yield. This can be done by cleaning the holes with a smaller drill, applying grease, and running an abrasive mix for 20–40 minutes.
**2.4 Feeding Scraper**
A worn feeding scraper can reduce the amount of material entering the die, leading to lower yield and higher powder content. Regular maintenance is necessary to ensure proper operation.
**2.5 Die Hole Clogging**
Clogging can occur due to poor granulation performance, unpolished molds, or residual oil. If clogged, the hole can be cleared with a drill, or the die can be soaked in oil and heated for easier removal.
**2.6 Friction Coefficient**
A low coefficient of friction between the material and the die/roller can cause slippage, reducing output. Conversely, a high coefficient can prevent material from being pressed out. Factors like formulation and conditioning affect this value.
**2.7 Feed Rate**
Even with skilled operators, a low feed rate will result in reduced output. Ensuring consistent feeding is key to maximizing yield.
**2.8 Cooling Process**
Insufficient cooling can lead to loose particles and increased powder. Proper cooling ensures stable pellet structure. The cooled pellet temperature should not exceed room temperature by more than 3°C.
**3. Machine Installation and Accessories Selection**
**3.1 Die Opening Rate**
A higher opening rate generally means higher production capacity. Larger hole diameters allow for better throughput, provided the die strength is maintained.
**3.2 Die Hole Shape**
Straight-hole ring dies are suitable for most compound feeds. However, for high-fiber feeds, tapered-hole dies may be more effective to maintain yield.
**3.3 Roll-to-Die Diameter Ratio**
A larger roll-to-die diameter ratio improves material flow and reduces backflow, enhancing yield. The ratio should be greater than 0.4.
**3.4 Scraper Position**
Improperly positioned scrapers can cause material loss and reduce output. The scraper edge should be 2–3 mm away from the die and cover, without extending into the die hole groove.
**3.5 Die Hole Aspect Ratio**
The depth-to-diameter ratio of the die hole influences both yield and hardness. For high-starch feeds, a ratio of 9.5–12.5 is ideal, while heat-sensitive materials require a lower ratio (4.8–8.0). Adding oil can help adjust this ratio for optimal performance.
Plano-Concave Cylinder Lens
Plano-concave cylinder lens, PCV Cylindrical Lens are commonly used to turn a collimated laser source into a line generator. The PCV Cylindrical lens and Illumination Grade Plano-Convex Cylindrical Lens can be used together for beam expander applications. Broadband Cylindrical lens feature precision specifications for the most demanding applications. Integration of these cylindrical lens is facilitated by square form factors allowing convenient mounting options. The cylindrical lens are widely used in the fields of medical, electronic, information, agriculture, communication and etc.
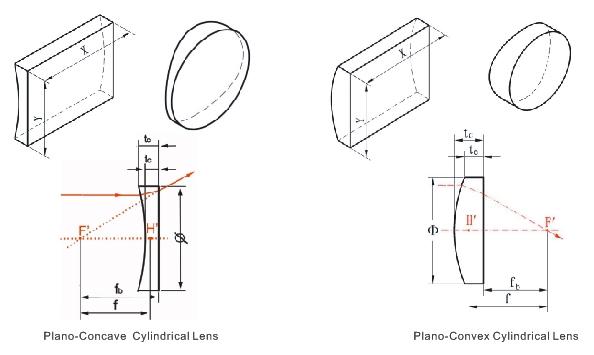
We supply kinds of plano-convex cylindrical lens,plano-concave cylinder lens,Double-Convex Cylinder Lens,Double-concave Cylinder Lens, Meniscus Cylinder Lens , Rod Cylinder Lens ,special cylindrical lens etc.
Specification of our cylinderical lens as follow:
*Material: BK7,Ge,UV-grade fuse silica(JGS1,JGS2,JGS3)or other optical materials
*Dimension Tolerance: +0.0 -- -0.1mm
*Center Thickness: +/-0.1mm
*Focal Length Tolerance: +/-1%
*Surface Quality:20/10
*Surface Figure: lambda/2 at 633nm on plano side
*Clear Aperture>90%
*Chamfer: 0.25mm at 45 degree typical
*Coating Optional
Plano-Concave Cylinder Lens,Plano Concave Lens,Mgf2 Plano-Concave Lens,Plano-Concave Cylindric Lens
China Star Optics Technology Co.,Ltd. , https://www.csoptlens.com