Due to the complexity of the foundry itself, I believe that the main problem in the energy-saving and material-saving sector is the formulation and implementation of the assessment rules.
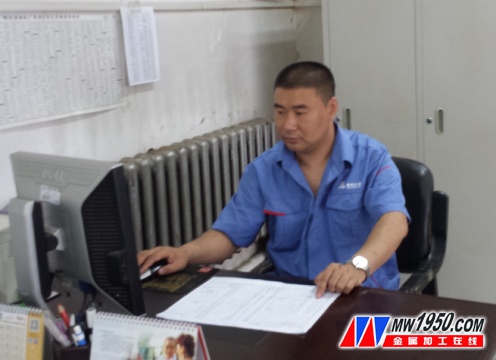
Harbin Electric Machinery Co., Ltd. Guan Junlong
Our factory is mainly engaged in large-scale steel castings. The annual production of castings is 6000-8000t. The main products are hydraulic crowns, lower rings, blades, vane-type stainless steel castings and silicon-manganese carbon steel castings. Our factory has done a lot of work in energy saving materials, specifically in the consumption of sand (chrome ore, silica sand), raw materials for welding skeleton (steel pipe, steel circle), smelting raw materials, natural gas consumption, electricity consumption, and improvement Casting process yield rate and other aspects.
With the fierce competition in the market, cost control is becoming more and more important. Due to the complexity of the foundry itself, I believe that the main problem in the energy-saving and material-saving section is the formulation and implementation of the assessment rules. In the implementation process, it is difficult to define the proportion of the cost of raw materials. For example, how to use raw materials such as sand and sand, how much energy consumption is the most reasonable, how to assess. At present, our factory is still in a process of continuous exploration, continuous improvement, and gradually becoming more reasonable. In recent years, our factory has increased cost assessment projects, actively promoted energy conservation and consumption reduction, per capita savings and cost reduction activities, and energy conservation and materialization. A hard assessment indicator for the target responsibility. The ultimate goal is to implement institutionalized management and form part of the corporate culture.
Process design is the basic technology of foundry enterprises. Reasonable use of cold iron and selective insulation riser in process design can reduce the total amount of molten steel; cold iron can be recycled after one-time investment; procurement cost and saving of thermal insulation riser The relationship between the cost of molten steel should be considered comprehensively; the application of process simulation can effectively test the process design, avoid waste of raw materials, and improve the probability of passing the process once. With the continuous popularization and application of casting simulation technology, the current process design has become simple, singular and efficient. Most craftsmen have listed how to meet the quality requirements as the first element, and should break the traditional process ideas, not only limited to the basic parameters of only the riser, cold iron, pouring system, machining allowance, sand type and tooling. It will continue to expand into three important factors: safety, cost, and practical production operability involved in the manufacturing process. Good process design requires us to consider quality, safety, cost, and actual production operability, because the purpose of the company is to pursue profit, and which factor will not cause control will cause losses.
The machining allowance is increased to increase the hot section of the casting, and the large-module riser is selected accordingly, which increases the amount of molten steel and increases the production cost. The purpose of casting is to meet the requirements of the use of parts. It is a basic forming process. At present, the process design is designed according to the manual or the standard of the unit to reserve the machining allowance. There is a certain generality. Reasonable and scientific processing allowance should be classified according to the product type: first, reduce the machining allowance according to the requirements of the use of the parts; secondly, improve the surface quality according to the sand raw materials and coatings of the enterprise to reduce the machining allowance; Design the sand core filling material to improve the concession and ensure that the casting size reaches the theoretical shrinkage to reduce the machining allowance.
The development direction of future casting technology should be guided by advanced technology, perfect computer numerical simulation technology, combined with 3D printing technology, closer to the actual production. It is necessary to fully consider safety and environmental protection, reasonable selection of casting raw materials, control of production operation process, pattern structure process and material selection, casting and solidification process simulation, so that the process design is more rationalized, the production process is more clear and clear, and the process design is improved. The accuracy and practical application ultimately achieve the purpose of improving quality and efficiency.
Brass Fitting For The Valve Element
Custom Valve Covers,Valve Element Brass Fitting,Forging Brass Faucet Body,Brass Fitting For The Valve Element
Jiangmen Xinhui Yilin Co.,Ltd , https://www.ylseiko.com